In the world of facility management, keeping operations running smoothly is paramount. Maintenance work order management efficiently plans, executes, and documents maintenance tasks through a systematic approach. By understanding what maintenance work order management entails, you can significantly enhance operational efficiency, reduce costs, and prolong the lifespan of your assets. In this blog post, we’ll delve into the key components, benefits, challenges, and best practices for effective maintenance work order management.
Introduction to Maintenance Work Order Management
Maintenance work order management refers to the process of planning, scheduling, tracking, and completing maintenance tasks within an organization. These tasks can range from routine inspections to emergency repairs, and they are vital to ensuring that all equipment and facilities operate as intended.
The primary purpose of maintenance work order management is to streamline the workflow associated with maintenance activities. Organizations minimize downtime, improve response times to issues, and ensure well-maintained assets. Effective management of work orders is not just about maintaining operations; it’s about optimizing the entire maintenance process for better efficiency and cost-effectiveness.
Key Components of Maintenance Work Order Management
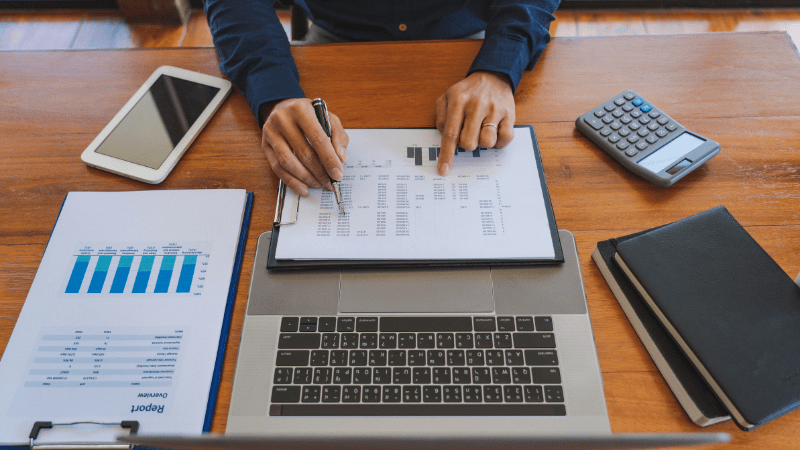
Understanding the key components of maintenance work order management is essential for implementing an effective system. These components include work order creation, assignment, tracking, and completion.
Work Order Creation
The first step in maintenance work order management is work order creation. A work order is typically initiated when a maintenance task needs to be performed. This could be due to routine inspections, preventive maintenance, or the sudden failure of equipment.
Work orders should include detailed information such as the asset in question, a description of the task, the priority level, and any other relevant details. Clear and accurate work order creation ensures that maintenance teams understand exactly what needs to be done.
Work Order Assignment
Create a work order and assign it to the appropriate personnel. Determine who is best suited for the task based on their skills, availability, and proximity to the asset.
Prioritization is also crucial at this stage. Not all maintenance tasks are of equal importance. Emergency repairs, for example, should take precedence over routine inspections. Proper assignment ensures that urgent issues are addressed promptly, while other tasks are scheduled in a manner that optimizes resource use.
Tracking and Monitoring
After the assignment, the work order moves into the tracking and monitoring phase. This is where real-time tracking of the work order’s progress takes place. Managers use tools like Computerized Maintenance Management Systems (CMMS) to monitor work order status and ensure timely resolution..
Tracking also involves updating the work order as tasks are completed or if any issues arise. Continuous monitoring helps in identifying bottlenecks or delays in the process, allowing for timely interventions.
Completion and Documentation
The final step is completion and documentation. Once the maintenance task is completed, the work order is closed. However, it is vital to document the details of the work done. This documentation includes what was fixed, how long it took, the resources used, and any follow-up actions needed.
Proper documentation not only helps in maintaining records for future reference but also provides data for analyzing the efficiency of the maintenance processes.
Benefits of Effective Maintenance Work Order Management
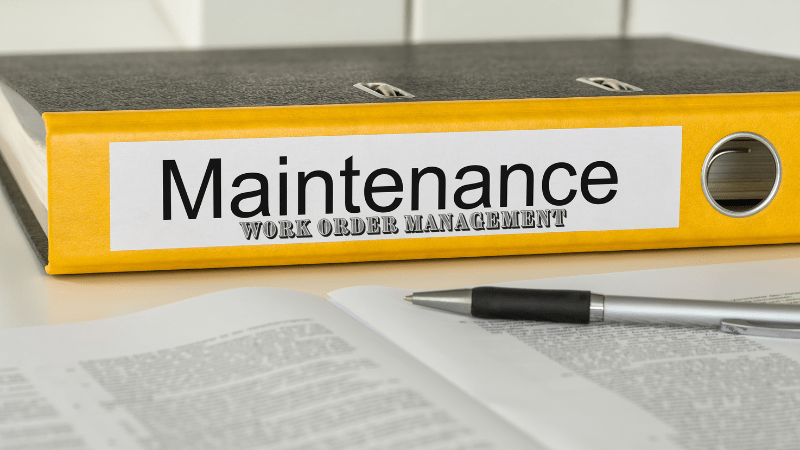
Implementing an effective maintenance work order management system brings several benefits to an organization. These benefits include increased efficiency, cost savings, improved asset management, and enhanced communication.
Increased Efficiency
By streamlining the maintenance process, work order management leads to increased efficiency. Maintenance teams can focus on their tasks without the burden of disorganized workflows. This efficiency reduces downtime and ensures that equipment is back online as quickly as possible.
Cost Savings
Effective work order management contributes to cost savings. By preventing small issues from becoming major problems, organizations can avoid expensive repairs and replacements. Additionally, optimizing resource allocation reduces waste and ensures that the right tools and personnel are used for each job.
Improved Asset Management
Improved asset management is another significant benefit. When work orders are managed efficiently, assets are maintained regularly and systematically, which prolongs their lifespan. Regular maintenance also helps in better forecasting future needs, allowing organizations to budget more accurately.
Enhanced Communication
Finally, work order management enhances communication within an organization. Clear work orders define expectations for maintenance teams, while real-time tracking and updates inform everyone about task status. This enhanced communication reduces the chances of miscommunication and errors.
Challenges in Maintenance Work Order Management
Despite its benefits, maintenance work order management can face several challenges. These challenges often arise from miscommunication, delays in processing, and inaccurate documentation.
Common Issues
Miscommunication between departments is a common issue in work order management. If maintenance teams do not receive clear instructions, tasks may be delayed or executed incorrectly. Additionally, delays in work order processing can slow down the entire maintenance process, leading to extended downtimes.
Another challenge is inaccurate or incomplete documentation. If the details in a work order are incorrect or missing, it can lead to confusion and inefficiencies. Proper training and standardized processes are essential to mitigate these challenges.
Overcoming Challenges
To overcome these challenges, organizations can implement several strategies. Effective communication tools are crucial in ensuring that all parties involved in the maintenance process are on the same page. Training staff on the importance of accurate data entry is also vital for maintaining the integrity of work orders. Additionally, using advanced software solutions can help streamline processes and reduce the likelihood of errors.
Tools and Software for Maintenance Work Order Management
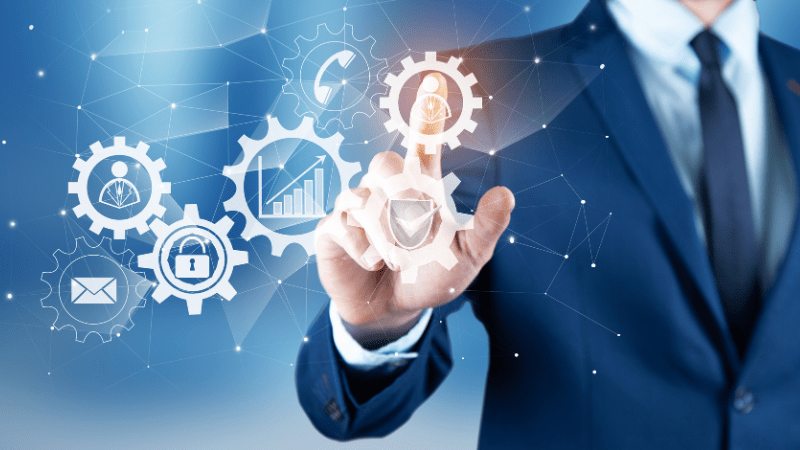
In today’s digital age, tools like Computerized Maintenance Management Systems (CMMS) play a pivotal role in effective work order management. CMMS software provides a centralized platform for creating, tracking, and managing work orders.
Computerized Maintenance Management Systems (CMMS)
CMMS software is designed to automate and streamline maintenance work order management. It allows organizations to track work orders in real time, monitor the status of tasks, and maintain a comprehensive database of maintenance activities. The software also facilitates better decision-making by providing valuable insights through analytics and reporting.
Mobile Work Order Management
With the advent of mobile technology, mobile work order management has become increasingly popular. Mobile access to work order systems allows maintenance teams to receive, update, and complete work orders on the go. This flexibility leads to quicker response times and greater efficiency.
Integration with Other Systems
Another advantage of modern work order management tools is their ability to integrate with other systems. Work order management links with inventory management, scheduling, and other enterprise systems. This integration coordinates all aspects of maintenance and optimizes resource use.
Best Practices for Effective Maintenance Work Order Management
To maximize the benefits of maintenance work order management, organizations should adhere to several best practices. These include standardization of processes, regular training, data-driven decision-making, and continuous monitoring.
Standardization of Processes
Standardizing work order procedures ensures consistency across all maintenance activities. Creating templates and guidelines helps in maintaining uniformity and reduces the chances of errors. This standardization is particularly important in large organizations with multiple teams and departments.
Regular Training and Updates
Continuous improvement is key to effective maintenance work order management. Regular training keeps staff members well-versed in the latest procedures and tools. Moreover, keeping systems and processes updated with the latest advancements helps in maintaining operational efficiency.
Data-Driven Decision Making
It is crucial to use data from work orders to make informed decisions. Data-driven decision-making allows organizations to identify trends, pinpoint inefficiencies, and implement corrective actions. Analytics and reporting tools within CMMS can provide valuable insights that drive better maintenance outcomes.
Continuous Monitoring and Improvement
Finally, organizations should adopt a culture of continuous monitoring and improvement. Regularly reviewing and updating work order processes ensures that they remain effective and relevant. Encouraging feedback from maintenance teams can also lead to innovative solutions and better practices.
FAQs
- What is a maintenance work order?
- A maintenance work order details a maintenance task, including the asset involved, task description, priority level, and assigned personnel.
- Why is work order management important?
- Work order management ensures efficient planning, execution, and documentation of maintenance tasks, improving operational efficiency, saving costs, and prolonging asset lifespan.
- How can work order management software help?
- Work order management software, such as CMMS, helps by automating the creation, tracking, and completion of work orders. It provides real-time insights, streamlines communication, and ensures accurate documentation.
- What are common challenges in work order management?
- Common challenges include miscommunication, delays in processing, and inaccurate documentation. Effective communication tools, proper training, and standardized processes mitigate these issues.
- How can NSPIRE Experts assist with work order management?
- NSPIRE Experts offers specialized services to help organizations implement and optimize work order management systems, providing solutions tailored to specific needs for improved efficiency and cost-effectiveness.
Conclusion
Maintenance work order management is a critical aspect of facility management that ensures the efficient operation of assets and equipment. Organizations can implement effective work order management systems that lead to increased efficiency, cost savings, and improved asset management by understanding the key components, benefits, challenges, and best practices.
NSPIRE Experts specializes in providing tailored solutions for maintenance work order management. Whether you need help implementing a CMMS system, training your staff, or optimizing your existing processes, NSPIRE Experts can guide you every step.