Maintenance Work Order Management
Maintenance Work Order Management Services
At NSPIRE Experts, we deliver reliable and efficient Maintenance Work Order Management services that help property managers and organizations streamline their operations, reduce downtime, and improve asset performance. Our goal is to provide a smart, structured workflow that ensures timely maintenance, optimal resource use, and clear accountability across your entire portfolio.
Whether you’re overseeing public housing, multifamily units, or commercial spaces, our maintenance work order management system supports every aspect of your operation—from request submission to task completion.
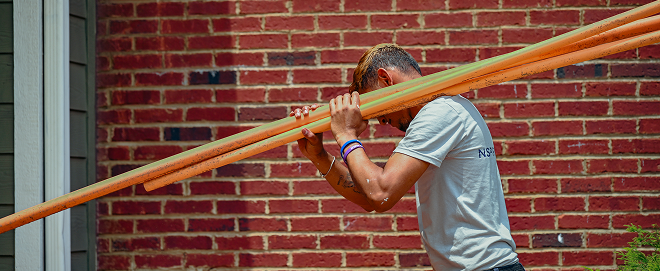
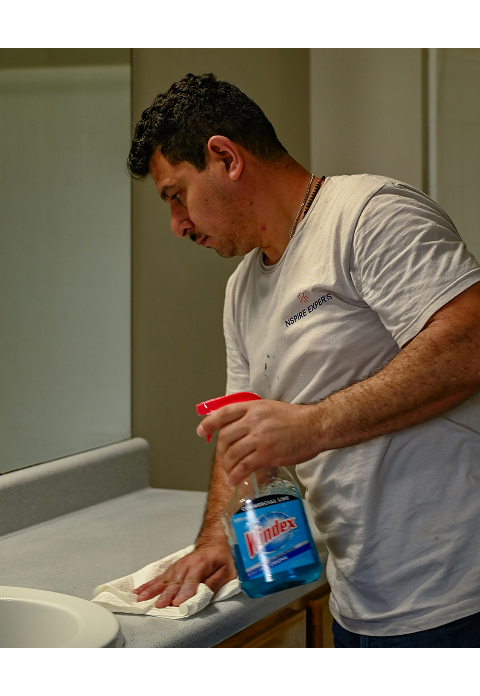
OUR SERVICE
Why Effective Maintenance Work Order Management Matters
- Efficient Task Tracking: We simplify how maintenance tasks are created, assigned, and completed, allowing your team to stay organized and responsive.
- Improved Operational Efficiency: By automating the flow of work orders, we reduce delays and ensure faster turnaround times on repairs and maintenance.
- Boosted Productivity: Our centralized system helps teams prioritize urgent tasks, reduce backlog, and maintain high service standards.
- Data-Driven Decisions: With real-time tracking and comprehensive reporting, you gain valuable insights into maintenance trends and performance metrics.
OUR PROCESS
Our Maintenance Work Order Management Process
Request Submission
Maintenance requests can be submitted online or via mobile, capturing key details like asset location, problem type, and urgency. This helps accelerate the entire process from the start.
Work Order Generation
Once a request is received, we generate a digital work order outlining all necessary steps, resources, and deadlines—ensuring every task is fully documented.
Assignment and Dispatch
Using real-time availability and skill-matching, we assign tasks to the right technicians and dispatch them immediately, reducing downtime and response delays.
Task Execution and Tracking
All work is monitored in real-time. Supervisors can view progress, provide support, and ensure standards are met, allowing for proactive issue resolution.
Documentation and Reporting
Each completed work order is documented with before/after details, technician notes, and time stamps. Performance reports are generated to support audits, future planning, and compliance tracking.
Feedback and Continuous Improvement
We continuously refine our process by gathering feedback from your team. This helps us identify gaps, improve workflows, and maintain the highest levels of service.

why choose us
Our Maintenance Work Order Management Services
Work Order Creation and Assignment
We make it easy to create and assign work orders using our intuitive platform.
Each task is prioritized and dispatched based on urgency, asset location, and technician availability—ensuring nothing gets overlooked.
Preventive Maintenance Scheduling
We proactively schedule preventive maintenance to avoid equipment failures and unexpected costs.
Our team uses predictive insights to reduce risks, extend asset life, and keep your properties running smoothly.
Inventory and Parts Management
Our services include streamlined inventory management so your teams always have what they need, when they need it.
We can even automate reorders based on usage history and current stock levels—avoiding costly delays.
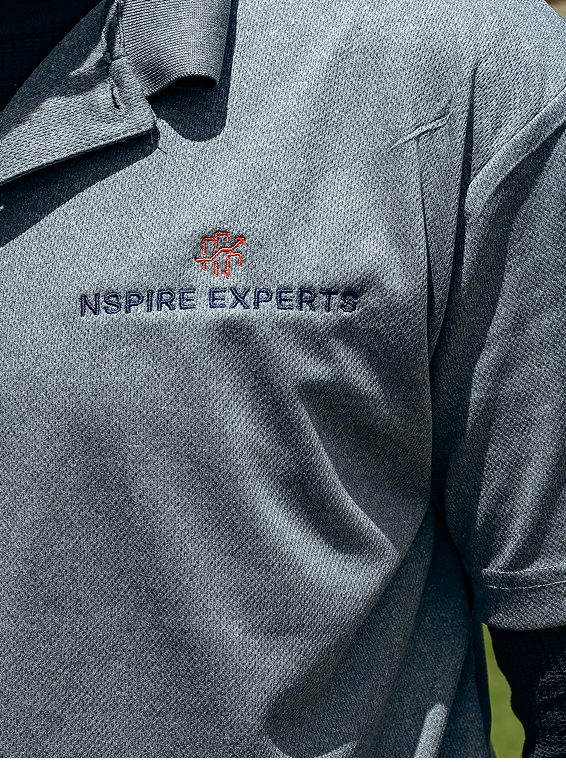
FAQs
Frequently Asked Questions
What is maintenance work order management?
It’s the process of organizing, assigning, and tracking maintenance tasks to ensure timely, efficient completion. A well-managed system helps extend asset life and keep operations running smoothly.
How does preventive maintenance fit into your workflow?
We schedule and track all recurring maintenance tasks, helping you reduce emergency repairs and plan for long-term asset upkeep.
Can NSPIRE Experts integrate with our existing system?
Yes. We can work with your current maintenance management software or implement our tools for seamless tracking and reporting.
How are work orders prioritized?
We prioritize based on urgency, safety, tenant impact, and asset condition. Critical issues are addressed immediately with smart technician dispatching.
Do you provide compliance and audit reporting?
Absolutely. All activity is logged, and custom reports are generated to support audits, track KPIs, and meet regulatory requirements.
How do we get started with your maintenance services?
NSPIRE Pre-Inspection
Let’s Optimize Your Maintenance Workflow
Ready to upgrade your operations with smarter Maintenance Work Order Management? NSPIRE Experts is here to streamline your tasks, improve turnaround time, and keep your property performing at its best.

Trusted by housing authorities and property managers nationwide

48-hour turnaround available

Nationwide service with flat-rate pricing
