Managing maintenance work order effectively is crucial for the smooth operation of any facility. At NSPIRE EXPERT, we understand the importance of a streamlined process that minimizes downtime and maximizes productivity. In this blog, we’ll outline eight essential steps for efficient maintenance work order management, ensuring your operations run like a well-oiled machine.
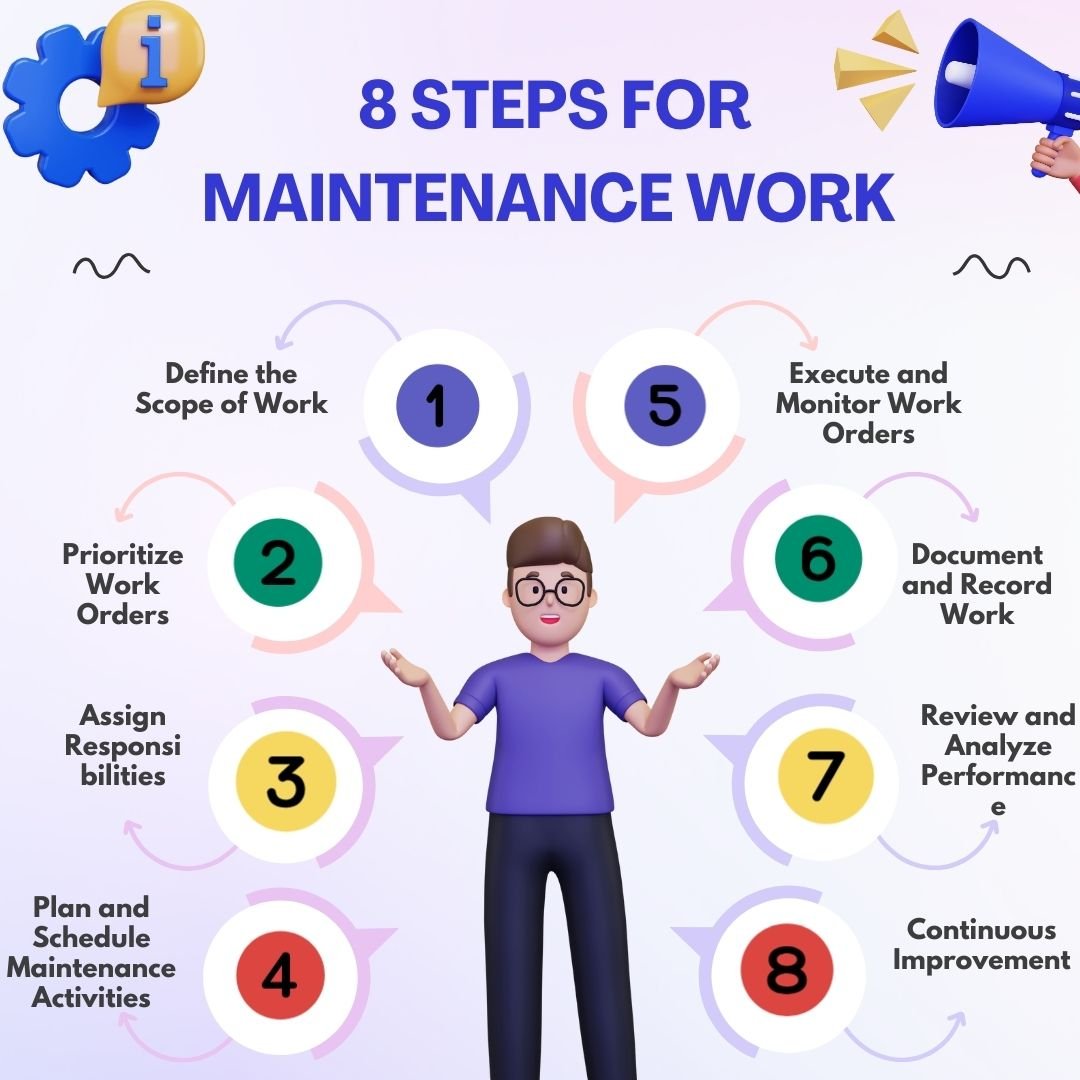
Step 1: Define the Scope of Work
The first step in maintenance work order management for home inspections is to clearly define the scope of work. This involves identifying the specific tasks that need to be performed, the equipment or area involve, and any special requirements. A well-defined scope helps avoid misunderstandings and ensures that all team members are on the same page.
Start by listing all required tasks in detail. For example, if the inspection involves checking the HVAC systems, specify whether it’s for regular servicing, part replacement, or troubleshooting a specific issue. Next, identify the equipment or areas involved. Knowing whether the maintenance is confine to a single unit or multiple systems across different locations helps in resource allocation. Finally, specify any special requirements or tools needed for the job. This thorough initial step is foundational for the success of your maintenance work order management process in home inspections.
- List all required tasks: Detail whether it’s regular servicing, part replacement, or troubleshooting.
- Identify involved equipment or areas: Understand the scope to allocate resources effectively.
- Specify special requirements or tools: Note if any unique tools or safety gear are neede.
Step 2: Prioritize Work Orders
Not all home inspection maintenance tasks are create equal. Prioritizing work orders is essential to ensure that critical issues are addresse promptly, while less urgent tasks are schedule accordingly. Use a priority matrix to categorize work orders based on urgency and impact.
Emergency work orders require immediate action due to safety concerns or significant operational impact. High priority tasks should be addresse within 24 hours to prevent minor issues from escalating. Medium priority tasks, which might not have an immediate impact but still need timely attention, should scheduled within a week. Low priority tasks, which have minimal impact on operations, can be schedule within a month. This structure approach ensures that resources are allocate efficiently, and critical issues are resolve promptly, enhancing the overall effectiveness of your maintenance work order management strategy.
- Emergency: Immediate action required due to safety or operational impact.
- High Priority: Address within 24 hours to prevent escalation.
- Medium Priority: Schedule within a week to maintain smooth operations.
- Low Priority: Plan within a month as they have minimal immediate impact.
Read it also : – What are the 7 Steps of Property Inspection Process?
Step 3: Assign Responsibilities
Effective maintenance work order management in home inspections requires clear assignment of responsibilities. Ensure that each work order is assigne to the appropriate technician or team with the right skills and availability. This step also involves setting deadlines and ensuring accountability.
Assign work orders to personnel who possess the necessary qualifications and expertise to handle the specific tasks. For instance, an electrical issue should be assigne to a certified electrician. Clearly define the deadlines for each task, making sure they are realistic and consider the technician’s workload. Establishing accountability is crucial; follow up with regular check-ins to ensure that tasks are on track and address any arising issues promptly. This structured delegation not only streamlines the maintenance process but also fosters a culture of responsibility and diligence.
- Assign to qualified personnel: Ensure technicians have the necessary skills.
- Set clear deadlines: Make realistic timelines considering the workload.
- Ensure accountability: Regular check-ins to track progress and resolve issues.
Step 4: Plan and Schedule Maintenance Activities
Once work orders are prioritized and assigne, the next step is planning and scheduling the maintenance activities. Utilize a maintenance management system to create a detailed schedule that takes into account the availability of resources, the time required for each task, and any dependencies.
A robust maintenance management software can help you map out the entire schedule, ensuring that tasks do not overlap and resources are utilize optimally. Consider the availability of necessary tools and spare parts, and coordinate with other departments to avoid disruptions. Account for task dependencies, such as completing electrical work before HVAC maintenance, to prevent delays. A well-planned schedule not only ensures timely completion of maintenance tasks but also enhances the overall efficiency of your maintenance work order management system.
- Use maintenance management software: Streamline scheduling and resource allocation.
- Coordinate resources: Ensure tools and parts are available when needed.
- Account for dependencies: Plan tasks in the correct order to avoid delays.
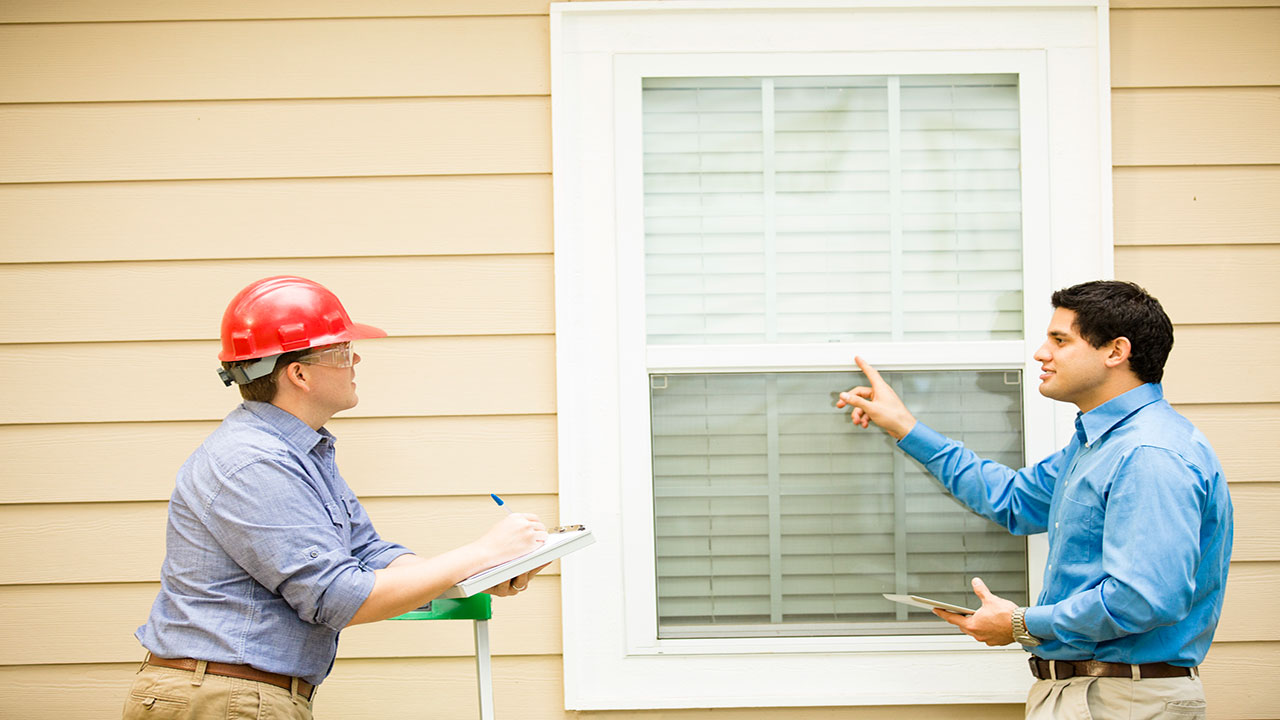
Step 5: Execute and Monitor Work Orders
Execution is where the rubber meets the road. Ensure that technicians have access to all necessary information, tools, and materials. Monitor the progress of work orders to ensure tasks are being complete on time and according to specifications.
Provide technicians with detailed instructions and all required resources before they begin the task. This includes manuals, safety guidelines, and access to necessary tools. Real-time monitoring through maintenance management software allows you to track progress and make adjustments as needed. Address any issues promptly to avoid delays. This hands-on approach ensures that maintenance tasks are execute efficiently, maintaining the integrity of your maintenance work order management process.
- Provide detailed instructions and resources: Equip technicians with everything they need.
- Monitor progress in real-time: Use software to track task completion.
- Address issues promptly: Solve problems quickly to stay on schedule.
Step 6: Document and Record Work
Thorough documentation is a key aspect of maintenance work order management. Record all completed work, including details of the tasks performed, materials used, and any issues encountered. This information is invaluable for future reference and continuous improvement.
After completing each task, document the specific activities performed. Include details about the materials and tools used, as this can help in planning future maintenance and budgeting for supplies. Record any issues encountered and how they were resolve. This documentation serves as a historical record that can be reference for similar future tasks, aiding in troubleshooting and improving maintenance procedures. Comprehensive documentation is essential for maintaining an efficient and transparent maintenance work order management system.
- Record tasks performed: Document activities for future reference.
- Note materials and tools used: Keep track of resources for budgeting.
- Document any encountered issues: Maintain a log of problems and solutions.
Step 7: Review and Analyze Performance
After completing the work orders, review and analyze the performance. Assess the efficiency and effectiveness of the maintenance activities and identify areas for improvement. Use metrics such as downtime reduction, cost savings, and task completion times to evaluate performance.
Gather data on key performance indicators (KPIs) to evaluate the success of your maintenance activities. Metrics like equipment downtime, cost savings from preventive maintenance, and the time taken to complete tasks provide insights into the effectiveness of your processes. Analyze this data to identify trends and areas needing improvement. For instance, if certain tasks consistently take longer than expected, investigate the root causes and adjust your processes accordingly. Regular performance reviews help in refining your maintenance work order management strategy, ensuring continuous improvement.
- Analyze efficiency and effectiveness: Use data to evaluate maintenance activities.
- Identify areas for improvement: Pinpoint where processes can be refine.
- Use performance metrics: Leverage KPIs to track and enhance performance.
Step 8: Continuous Improvement
Maintenance work order management is an ongoing process that benefits greatly from continuous improvement. Regularly review and update processes based on performance analysis, feedback from technicians, and changes in operational needs. Implementing best practices and staying adaptable are key to long-term success.
Schedule periodic reviews of your maintenance processes and seek feedback from your maintenance team. Their hands-on experience can provide valuable insights into potential improvements. Stay updated with industry best practices and incorporate them into your procedures. Adapt to changes in your operational environment, such as new regulations or technological advancements, to keep your maintenance practices current and effective. Emphasizing continuous improvement ensures that your maintenance work order management system remains robust and responsive to evolving needs.
- Regularly review and update processes: Ensure procedures are current and effective.
- Implement feedback and best practices: Use insights from your team and industry standards.
- Adapt to changing needs: Stay flexible to new regulations and technologies.
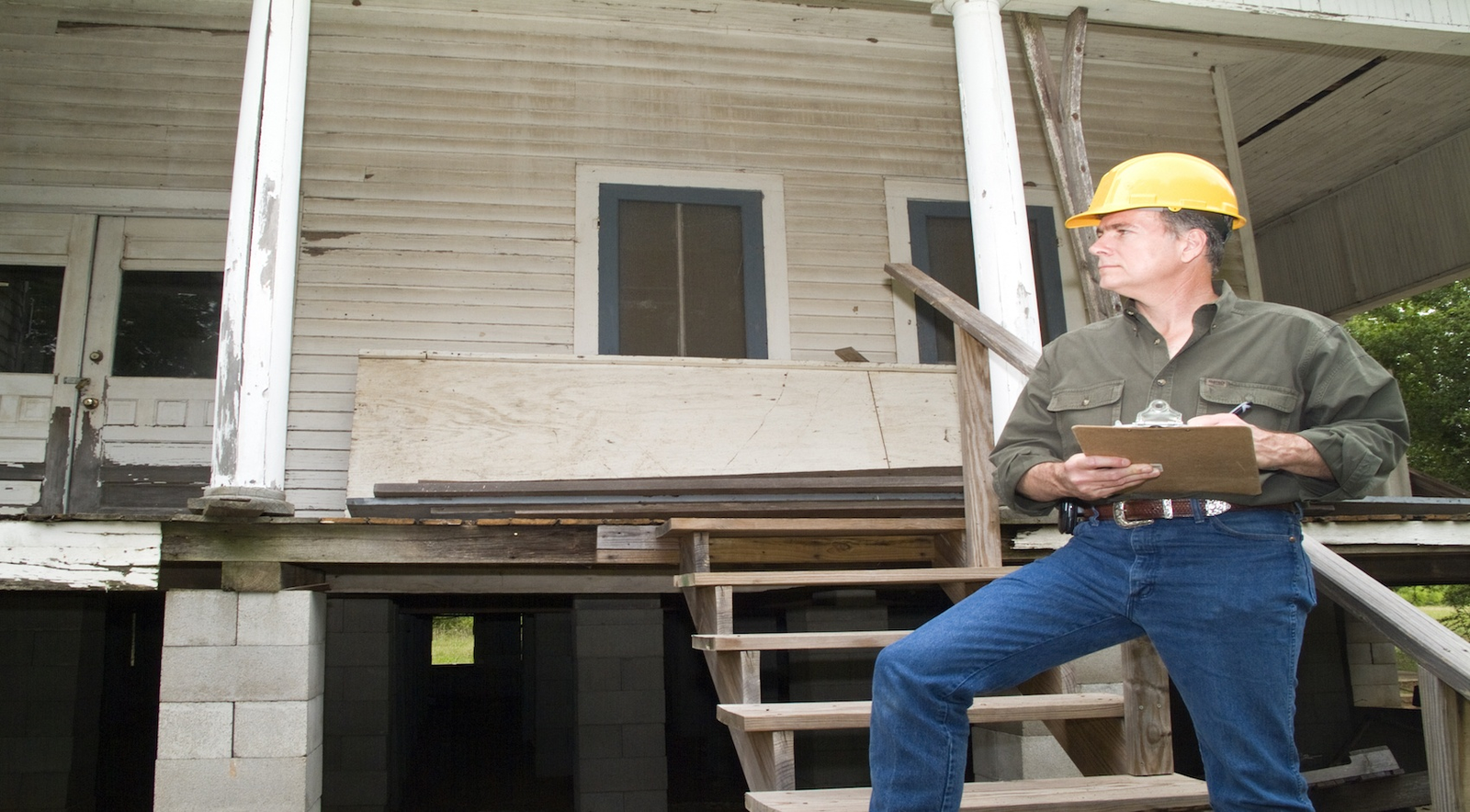
Contact Us
At NSPIRE EXPERT, we specialize in providing top-notch maintenance work order management solutions tailored to your specific needs. If you’re looking to optimize your maintenance processes, contact us today!
Email: Info@nspireexperts.com
Phone: (866) 516-7322
Efficient maintenance work order management not only enhances productivity but also ensures the longevity of your equipment and facilities. By following these eight steps, you can create a seamless process that addresses issues promptly, minimizes downtime, and fosters continuous improvement. Reach out to NSPIRE EXPERT for expert assistance and take your maintenance management to the next level.